Infrastructure Monitoring with InfluxDB | Live Demonstration
Predictive Maintenance
Predictive Maintenance is a maintenance strategy that uses a combination of sensors and data analysis to detect issues in machinery or other equipment before they become major problems.
What is predictive maintenance?
Predictive Maintenance is a maintenance strategy that uses a combination of sensors and data analysis to detect issues in machinery or other equipment before they become major problems.
The objective of predictive maintenance is to reduce the amount of unplanned downtime and increase the lifespan of the equipment being monitored. This results in more efficient operations, higher productivity, and improved business outcomes for the businesses that are utilizing predictive maintenance.
How does predictive maintenance work?
The first step of predictive maintenance is the implementation of sensors. These sensors collect data that is used for analysis to identify patterns that can be used to predict breakdowns in machinery before they occur. Analysis techniques can include machine learning models or traditional statistical methods for anomaly detection.
Once enough historical data has been collected to make reliable predictions, workers can begin to shut down equipment or make repairs before issues occur, rather than having to wait before taking action.
A real world example of this could be monitoring the vibration levels of a motor. Predictive maintenance algorithms can analyze this data and alert the maintenance team that a bearing may be starting to wear out based on the data from the sensor. The team can then schedule maintenance to replace the bearing before it fails, which minimizes downtime and prolongs the life of the machine compared to waiting for it to fail.
Predictive maintenance benefits
Let’s look at some more benefits of using predictive maintenance:
-
Increased lifespan of machinery - Predictive maintenance can help organizations to increase the lifespan of their machinery or equipment by proactively detecting potential problems before they become significant issues.
-
Reduced downtime and better efficiency - Predictive maintenance can reduce unplanned downtime by allowing machinery repairs to be made proactively. This makes factories more efficient by allowing them to operate at full capacity more often.
-
Worker safety - In workplaces where machine failure could cause injury to workers, being able to more accurately predict failures helps keep workers safe.
Predictive maintenance challenges
While predictive maintenance can provide a number of benefits like those covered earlier, that doesn’t mean it’s perfect. There are a number of challenges to implementing and using predictive maintenance successfully in production. In this section you will learn about some of the most common issues.
Data quality
For predictive maintenance to work, above all else you need data that is accurate. That means making sure sensors are calibrated properly, data isn’t missing, and the data is representative across all hardware being monitored.
Collecting and integrating data
Once data is being generated, another common issue is integrating all that data coming from different sources into something usable for building a model or generating alerts.
This will typically involve some sort of ETL pipeline to transform and move data for long-term storage. Storage for this type of data needs to be able to efficiently compress the data while also serving queries quickly to make it usable. Common tools used for storage are time series databases, data warehouses, or columnar databases.
Prediction algorithm development and selection
Once data is stored, you need to choose how to analyze that data to gain insights. Models can be designed from scratch with data science techniques like feature engineering, or you can pick pre-existing algorithms that have proven to work for similar types of problems.
Algorithm selection is important because it will determine how accurate the predictions are, how quickly they can be generated, and the cost of hardware needed to make these predictions.
Company culture
Implementing predictive maintenance can require major changes to existing processes and workflows. For predictive maintenance to be effective, leaders will need to make sure their workers buy into the new system.
Implementation and maintenance costs
Startup costs for predictive maintenance can be high due to the need to install sensors, create software to process data, and train employees to utilize the new system.
Once the system is in place, there will be continued costs to maintain it. Sensors will need to be cleaned, repaired, or replaced to ensure they continue collecting accurate data.
False positives
False positives from inaccurate predictive maintenance algorithms can not only result in wasted maintenance costs, but also cause workers to lose confidence in the system.
Predictive maintenance use cases and industries
Predictive maintenance can be used for a wide variety of things, but here are a few specific use cases to help you get some ideas about how it is currently being used in the real world:
-
Automotive fleet management - Predictive maintenance can be used for tracking the status of vehicles and predict when they need maintenance or repair for various components. This will reduce the lifetime cost of the vehicle and save money for the owner.
-
Industrial machinery - Predictive maintenance is used in industrial settings to monitor the performance of equipment such as pumps, motors, and generators. This can help to reduce the amount of unplanned downtime and keep operations running smoothly.
-
Power generation - Various equipment like turbines and generators can benefit from predictive maintenance. By knowing when things need to be repaired or are in danger of failing, electrical companies can know what kinds of infrastructure investments they need to make and provide more reliable service to customers.
-
Construction and infrastructure - Properly implementing predictive maintenance for things like buildings, bridges, and roads can help prevent catastrophic failures and help make cheap fixes before they become expensive repairs.
Technologies used for predictive maintenance
There are a number of different ways to collect data for predictive maintenance. In this section we will look at some of the more common methods used to test equipment for predictive maintenance.
Infrared analysis
Infrared cameras are commonly used for predictive maintenance. These cameras can be used to find abnormal temperature readings that might indicate a problem with the equipment. This process can be done manually by employees or automated using new AI-powered image recognition systems.
Electric signal monitoring
This involves monitoring the electrical signals of equipment to detect changes that may indicate problems. For example, changes in the voltage or current signals may indicate a problem with a motor or generator.
Acoustic analysis
Acoustic monitoring involves using equipment to record sounds being emitted by equipment at the sonic and ultrasonic level. Examples include listening for gas leaks and detecting issues with engines. Ultrasonic monitoring is particularly useful because it can detect things outside human hearing ranges to determine things that signal abnormalities in equipment.
Vibration analysis
Vibration analysis is used for monitoring high-speed rotating equipment. A baseline reading can be recorded while the equipment is in ideal condition to determine the normal vibrational rhythm. If the machinery starts to deviate from this rhythm, it is a sign that repairs or adjustments need to be made.
In many cases the change in vibrations emitted by equipment can be used to know exactly what the problem is based on historical data, for example the difference in readings caused by loose parts vs motor issues. This makes repairs faster because the technician knows exactly what they need to fix rather than having to do exploratory analysis of all equipment components.
Fluid analysis
Another common part of a successful predictive maintenance program is fluid analysis. This involves tracking the physical and chemical aspects of fluids used in machinery like coolants or lubricants. This allows for optimizing replacement for these fluids and prevents waste. It also allows for preventive maintenance to be coordinated to take place at the same time the equipment is already being taken out of operation for fluid replacement.
Condition based monitoring
Condition based monitoring is the collection of data that gives the current condition or performance of the equipment being monitored. This includes things like temperature or pressure.
Visual inspection
Visual inspection involves looking at equipment for signs of damage like cracks or corrosion. With modern AI image recognition, this process can be somewhat automated and done with more frequency.
Predictive maintenance vs. inspection for defects
The main difference between predictive maintenance and inspection for defects is that predictive maintenance uses data to predict when an issue may arise, while inspection for defects is used to identify existing issues. Predictive maintenance can be more effective at reducing unplanned downtime and identifying potential problems before they become significant.
Predictive maintenance FAQs
What is the difference between predictive maintenance, preventive maintenance, and reactive maintenance?
There is quite a bit of overlap between the different types of maintenance. Here is a summary of each and some of the differences:
-
Predictive maintenance - This type of maintenance uses sensors, data analysis and other technologies to monitor equipment performance in order to predict and identify potential problems before they become significant.
-
Preventive maintenance - Preventative maintenance involves regularly scheduled inspections, repairs, and replacements that are designed to keep equipment running at optimal levels. The downside is that it isn’t as efficient due to being standardized around set schedules rather than optimized based on precise data for each machine.
-
Reactive maintenance - Reactive maintenance is used when a problem or malfunction occurs and requires immediate attention. Reactive maintenance is usually more expensive than other types of maintenance because it is often done on an emergency basis.
When does it make sense to use predictive maintenance?
Predictive maintenance makes sense when some of the following conditions are true:
-
Equipment is valuable in terms of direct cost or if downtime will impact overall productivity of your business.
-
Equipment has high maintenance costs or requires a specialist to repair.
-
Equipment is critical to the safety of workers or citizens.
On the other hand if the equipment is cheap to replace, has low failure rates, or isn’t critical to safety or operations, it might not be worth the effort and expense to set up monitoring and related things needed for predictive maintenance.
How does Predictive maintenance relate to the Internet of Things (IoT)?
The Internet of Things (IoT) is the connection of devices to the internet, allowing for communication and data exchange between them. Predictive maintenance can leverage IoT technology in order to monitor and analyze connected devices in real time.
What is condition monitoring?
Condition monitoring is the process of continuously monitoring the operating conditions of equipment to detect changes that may indicate potential problems. It involves using sensors and other monitoring equipment to collect data on key performance indicators (KPIs) such as temperature, vibration, pressure, and flow rate. By analyzing this data, it’s possible to identify changes that may indicate wear and tear, damage, or other issues.
Condition monitoring is closely related to predictive maintenance because it’s a key component of many predictive maintenance programs. In order to implement an effective predictive maintenance program, it’s important to have accurate and reliable data on the condition of equipment. This data can be used to identify trends, predict failures, and schedule maintenance activities before a breakdown occurs.
Take charge of your operations and lower storage costs by 90%
Get Started for Free Run a Proof of ConceptNo credit card required.
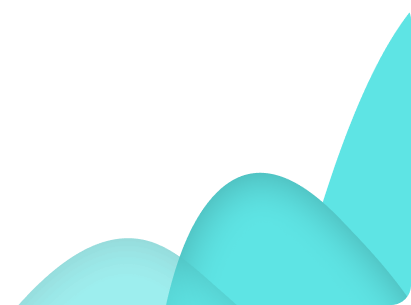