Infrastructure Monitoring with InfluxDB | Live Demonstration
Overall Equipment Effectiveness (OEE)
Overall Equipment Effectiveness (OEE) is a metric for measuring manufacturing productivity
What is OEE?
Overall Equipment Effectiveness (OEE) is a metric for measuring manufacturing productivity. It considers three factors: availability, performance, and quality to provide a comprehensive view of equipment effectiveness. By tracking OEE, manufacturers can identify areas for improvement and take action to optimize their manufacturing processes.
How is Overall Equipment Effectiveness used?
Overall Equipment Effectiveness (OEE) is used to evaluate how efficiently a manufacturing process is running. By measuring and tracking OEE, manufacturers can identify production losses and areas for improvement. OEE is also used as a benchmark for comparing performance across different manufacturing plants or production lines.
Overall Equipment Effectiveness is used by manufacturers to measure the performance and productivity of their manufacturing equipment. By measuring the OEE of equipment, manufacturers can identify areas of inefficiency and waste, and make data-driven decisions to improve their manufacturing processes.
OEE is a critical tool for industrial automation engineers and managers to optimize the performance of their manufacturing equipment and increase productivity. OEE can be used to identify the root causes of production losses and implement targeted solutions to address them. It can also be used to track progress towards improvement goals and to compare the performance of different equipment or facilities. OEE can be applied in a wide range of manufacturing settings, including automotive, food and beverage, pharmaceuticals, and many others.
OEE benchmarks
An elite OEE score is considered to be 85% or higher. However, the average OEE score across all industries is around 60%. It’s important to note that OEE benchmarks can vary depending on the type of industry and manufacturing process. Discrete manufacturers for example typically have lower OEE scores due to the complexity of their production processes.
OEE Benchmark | Range of OEE |
---|---|
Elite | 85% - 90% |
Good | 60% - 85% |
Average | 40% - 60% |
There are generally three common benchmarks used to evaluate the OEE of manufacturing equipment: Elite, Good, and Average.
Elite OEE
This benchmark represents the highest level of OEE that can be achieved by manufacturing equipment. A World Class OEE typically ranges from 85% to 90%, and is achieved by only a few top-performing manufacturers. Achieving this level of OEE requires a high degree of efficiency and optimization across all aspects of the manufacturing process, including availability, performance, and quality.
Good OEE
This level of OEE is achievable by most manufacturers with some level of effort and improvement. A good OEE typically ranges from 60% to 85%, and requires a focus on optimizing the manufacturing process to reduce waste, downtime, and defects. Achieving a Good OEE involves balancing the trade-offs between availability, performance, and quality, and making incremental improvements to each area over time.
Average OEE
This benchmark is the typical OEE level that is observed in manufacturing facilities, and can range from 40% to 60%. Achieving this level of OEE often involves identifying and addressing common sources of waste and inefficiency, such as excessive downtime, long changeover times, and poor quality. An average OEE indicates that there is significant room for improvement in the manufacturing process and that there are likely opportunities to increase productivity and reduce costs by optimizing the equipment’s performance.
How to Calculate Overall Equipment Effectiveness (OEE)
There are several different factors that go into calculating OEE. In this section we’ll look at these different values that need to be taken into account and then look at how they impact overall OEE scores.
Availability calculation
Availability is the ratio of actual production time to planned production time. It is calculated by dividing the actual production time (minus any unplanned downtime) by the total planned production time.
Availability = Actual production time / Planned production time
Performance Calculation
Performance is the ratio of actual production count efficiency to the maximum possible speed. It is calculated by dividing the actual production count (minus slow cycles) by the theoretical maximum production count, which is based on the maximum possible speed of the equipment.
Performance = Actual output / Maximum potential output
Quality Calculation
Quality is the ratio of good units produced to total units produced according to quality control standards for the product being made. It is calculated by dividing the number of good units by the total number of units produced.
Quality = Good output count / Total output count
OEE Calculation
Overall Equipment Effectiveness is calculated by multiplying the availability, performance, and quality scores. The resulting OEE score is expressed as a percentage.
OEE = Availability x Performance x Quality
What Are the Six Big Losses When It Comes to Overall Equipment Effectiveness?
One of the key benefits of OEE is that it can help manufacturers identify the sources of production losses that are reducing the efficiency and productivity of their equipment. There are six big losses that are commonly used to categorize the sources of production losses, and which can be targeted for improvement using OEE.
Equipment Failure
Equipment failure refers to instances when equipment breaks down or malfunctions. This can result from machinery wear, tooling failure, or incorrect machine settings. Equipment failure can cause unplanned downtime and reduce the availability score.
Setup & Adjustment
Setup and adjustment losses occur when equipment is being prepared for production or adjusted during production. This may include changeovers between different products, general maintenance, or calibration. These losses contribute to reduced availability.
Idling & Minor Stops
Idling and minor stops are short, unplanned stops in production. They may be caused by equipment jams, misfeeds, or operator intervention. These losses reduce the performance score.
Reduced speed
Reduced speed losses occur when equipment operates at a slower pace than the maximum possible speed. This may result from wear, poor maintenance, or external factors like not having necessary inputs for manufacturing at full capacity. Reduced speed affects the performance score.
Process Defects
Process defects are units that do not meet quality standards due to issues in the manufacturing process. These defects may be caused by equipment malfunction, poor process design, or operator error. Process defects reduce the quality score.
Yield losses
Yield losses occur when the production process generates waste or produces units that cannot be sold. This may be due to equipment inefficiency, poor process design, or substandard materials. Reduced yield affects the quality score.
By categorizing production losses into these six big losses, manufacturers can better understand the root causes of inefficiencies and waste in their production processes. This allows them to implement targeted improvements to address these sources of production losses and increase the overall efficiency and productivity of their manufacturing equipment.
Benefits of OEE
Implementing OEE in a manufacturing environment offers several benefits, including:
Reduced costs
By identifying and addressing the sources of production losses, manufacturers can reduce equipment downtime, maintenance costs, and waste, leading to lower overall costs.
Improved workforce productivity
Tracking OEE can help managers identify areas where operators may need additional training or support, leading to an increase in workforce productivity.
Reduced downtime
By monitoring equipment performance and implementing preventive maintenance strategies, manufacturers can minimize unplanned downtime and maximize equipment availability.
Improved product quality
By identifying and addressing process defects, manufacturers can improve product quality and reduce waste.
How to get started with implementing OEE?
If you are looking to implement OEE in your manufacturing process the following steps are a simple guideline for getting started.
- Determine the key performance indicators (KPIs) for your manufacturing process- Identify the metrics that are most important to measure the performance of your manufacturing equipment, such as availability, performance, and quality, which are standard across industries for measuring OEE. Beyond those basic KPIs you can add any additional metrics and track to see how they are impacted by OEE as well. These KPIs will serve as the basis for calculating OEE and tracking improvements.
- Establish a baseline OEE score- Calculate the OEE for a representative period of time, such as a shift, a day, or a week. This baseline OEE score will provide a starting point for measuring progress and identifying areas for improvement.
- Identify areas for improvement- Conduct a detailed analysis of the sources of production losses, such as downtime, changeovers, and defects. Use tools such as Pareto charts and fishbone diagrams to identify the most significant sources of waste and inefficiency.
- Develop and implement strategies for addressing the identified areas for improvement- Develop specific action plans and initiatives to fix the identified sources of waste and inefficiency. These strategies may include process improvements, equipment upgrades, or training programs for operators.
- Continuously monitor OEE and track progress towards goals- Regularly monitor and report OEE performance to ensure that progress is being made toward improvement goals. Use real-time monitoring systems and data analytics tools to identify opportunities for further optimization and improvement.
Tools for OEE Monitoring
There are several tools available for OEE monitoring, including software solutions and dedicated hardware devices. These tools can help automate the data collection and calculation processes, making it easier for manufacturers to track and analyze OEE metrics.
Common OEE challenges
Some common challenges associated with implementing an OEE system include:
- Establishing accurate benchmarks for comparison- Setting accurate benchmarks for OEE can be challenging, as there may be significant variation between different types of manufacturing processes and equipment. Manufacturers may need to rely on industry standards or benchmarking against similar facilities to establish appropriate benchmarks.
- Ensuring consistent data collection and reporting- Collecting and reporting accurate data on the factors that contribute to OEE can be challenging. Manufacturers need to ensure that their data collection methods are consistent and reliable, and that their reporting processes are standardized and accessible to all relevant stakeholders. If this isn’t done properly decisions might be made based on a false vision of reality.
- Addressing cultural resistance to change- Implementing OEE requires changes to processes, equipment, and employee behaviors which can be met with resistance from workers and managers. Manufacturers need to address this by communicating the benefits of OEE and involving employees in the improvement process.
- Integrating OEE with other systems and processes- Integrating OEE with other manufacturing systems, such as maintenance management or enterprise resource planning (ERP) systems, can be challenging. Manufacturers need to ensure that their OEE systems are compatible with their existing systems and that data is shared effectively across different departments and functions.
- Balancing OEE with other business objectives- While improving OEE can lead to increased productivity and profitability, manufacturers need to balance OEE improvements with other business objectives, such as product quality, safety, and customer satisfaction. This requires a strategic approach to OEE implementation that takes into account the broader goals of the organization.
OEE best practices
To maximize the benefits of OEE, here are some best practices to consider:
Engage employees at all levels of the organization
Effective OEE implementation requires the engagement of employees at all levels of the organization. This involves providing training and education on OEE concepts and involving employees in the improvement process through brainstorming sessions, improvement teams, and regular communication.
Regularly review and update OEE goals and strategies
OEE goals and strategies should be reviewed and updated on a regular basis to ensure continuous improvement. This requires regular monitoring of OEE data, the identification of new opportunities for improvement, and the adjustment of goals and strategies as needed.
Focus on root cause analysis
Use root cause analysis to identify the underlying causes of production losses and implement targeted solutions to address them.
Implement visual management tools to improve transparency and communication
Use visual management tools such as dashboards and scorecards to improve transparency and communication throughout the organization.
Establish a cross-functional team to lead OEE implementation
Establish a team of representatives from different departments to lead OEE implementation. This team should have the authority and resources to drive OEE improvements throughout the organization.
FAQs
What is perfect production?
Perfect production is a hypothetical scenario in which equipment operates at 100% availability, 100% performance, and 100% quality. In this scenario, the OEE score would be 100% and the manufacturing facility would be producing good at maximum capacity.
What is TEEP?
Total Effective Equipment Performance (TEEP) is a similar metric to OEE that includes the utilization factor, which considers the proportion of time that equipment is scheduled for production. TEEP provides a more comprehensive view of equipment effectiveness by accounting for both productive and non-productive time.
How does task loading relate to Overall equipment effectiveness?
Task loading refers to the allocation of tasks or workload to a piece of equipment. A high task loading can result in increased equipment wear, reduced performance, and an overall decrease in OEE.
What is the average ROI for implementing Overall Equipment Effectiveness?
The average ROI for implementing OEE varies depending on factors such as the size of the manufacturing facility, the complexity of the production process, and the level of investment in OEE improvement initiatives. However, studies have shown that manufacturers can achieve significant cost savings and productivity improvements by implementing OEE.
How does OEE relate to Industry 4.0?
OEE is closely related to the Industry 4.0 movement, which seeks to digitize and optimize industrial processes through the use of advanced technologies such as the Internet of Things, big data analytics, and artificial intelligence. OEE is a critical component of Industry 4.0, as it provides a comprehensive measure of the efficiency and effectiveness of manufacturing equipment, which can be used to optimize production processes and increase overall equipment reliability.
OEE can be integrated with other Industry 4.0 technologies, such as predictive maintenance systems, which use machine learning algorithms to predict equipment failures before they occur, and digital twin technology, which creates a virtual model of manufacturing equipment that can be used to optimize its performance.
Take charge of your operations and lower storage costs by 90%
Get Started for Free Run a Proof of ConceptNo credit card required.
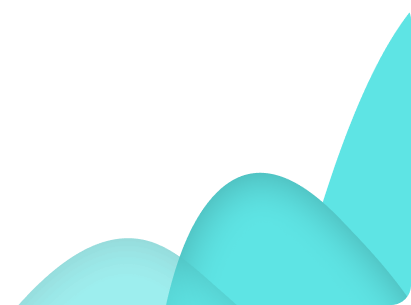