Infrastructure Monitoring with InfluxDB | Live Demonstration
Digital Twins
A digital twin is a virtual model or replica of a physical object, process, or system that is used for simulation, analysis, and understanding.
What is a digital twin?
A digital twin is a virtual model or replica of a physical object, process, or system that is used for simulation, analysis, and understanding. Digital twins are a key component for the Internet of Things and works to pair the virtual and physical worlds. This overall concept is a key part of what is known as the “digital transformation”
Digital twins are created to mirror and mimic their physical counterparts in every way possible. This includes not just the structure or appearance, but also the dynamics and behavior under certain conditions.
Once a digital twin has been created, it can be used for tests and analysis that would be expensive, time-consuming, or potentially harmful in the real world. This allows for problem-solving, prediction, and planning for the future without any risk to the actual physical counterpart.
How does a digital twin work?
Digital twins work by creating a dynamic digital representation of a physical object or system. This begins with the collection of data from various sources, typically sensors embedded in the physical object. This data might include information about the object’s physical properties, behavior, location, environment, and more.
This data is then fed into a digital model that represents the physical object in a virtual environment. Advanced software algorithms are used to process and analyze the data, providing a real-time simulation of the physical object’s behavior. The digital twin is then able to mirror the real-world object or process, reflecting its current state, past performance, and even predicting future outcomes.
One of the key benefits of digital twins is the ability to run simulations and what-if scenarios. You can change variables in the digital twin to see how the physical object would respond under different circumstances. This ability to simulate and predict outcomes without risking the physical object or system is a core value of digital twins.
In short, digital twins work by integrating real-time data from a physical object with a virtual model, enabling real-time analysis, prediction, and simulation to support decision-making, process optimization, and innovative solutions. The constant feedback loop between the digital twin and the physical object allows the twin to learn and adapt, mirroring changes in the real-world counterpart.
What Is the History of Digital Twins?
Digital twins as a concept goes back to the 1960s where engineers at places like NASA realized the value in computer simulations for testing hardware. This type of simulation was mostly used by the aerospace and defense industries over the following decades.
The term “digital twins” was popularized in 2002 by Michael Grieves, a professor at the University of Michigan. Digital twins quickly grew in adoption as a way to improve product lifecycle management. This adoption was accelerated as computer hardware improved and got cheaper, leading to the rise of IoT. The ability to handle large volumes of real time data that could be integrated with digital twin models led to adoption across many more industries like manufacturing, healthcare, urban planning, and retail.
Recent advancements in digital twin technology have integrated things like data analytics, machine learning, and AI to improve the capabilities of digital twin models. Real time data allows digital twin models to be dynamic and change with data coming from their physical counterpart.
Digital twins benefits
Improved efficiency and productivity
Businesses can streamline their operations by modeling different scenarios using digital twins. This allows for processes to be simulated before implementation to test their impact, which can reduce mistakes and thus cost.
Enables better predictive maintenance
Digital twins can be used to predict defects before they occur in the physical twin. This can prevent downtime, improve reliability, and prevent costly recalls for defective products. Predictive maintenance can be used by testing a digital twin under a variety of different conditions, so maintenance costs can also be reduced by doing repairs before equipment breaks down completely.
Faster innovation
By providing a risk free environment for experimentation, innovation is easier as well as faster due to iteration speed. New designs, strategies, or systems can be tested out without having to worry about destroying expensive equipment, materials, or impacting existing operations.
Improved decision making
Because digital twins can deliver real time data and insights, business leaders can make more informed decisions for strategic planning.
Easier training
Digital twins can be used for practice and training in high risk industries like aerospace and healthcare. Workers can get hands on experience without risking equipment or other people. It also allows for higher volumes of training that simply might be possible with traditional training.
Digital twin challenges
Data management
To create and use digital twins effectively you need to be able to collect, process, store, and analyze large amounts of data. This requires sophisticated software systems and engineers to manage them.
Integration
To collect the data needed you will need to be able to integrate existing physical systems to your software. This will involve deploying and managing large numbers of IoT devices and building a network to transfer data.
Security
Much of the data being generated by these systems is sensitive from both a business perspective and potentially regulatory perspective as well depending on industry. As a result security is a critical challenge that needs to be addressed when building a digital twin system. A system must be designed to prevent data breaches and also ensure compliance with privacy laws and regulations.
Implementation cost and complexity
Underlying all the previous challenges are the cost and complexity. The hardware itself can be expensive to deploy, maintain, and upgrade over time. Building a digital twin will also require a large number of employees with specialized skills for both hardware and software engineering.
Digital twin use cases
There are a number of potential use cases for digital twins across a variety of industries. Here are some of the most common use cases for digital twin technology.
Manufacturing
Digital twins can simulate a production line, allowing operators to detect inefficiencies and test potential improvements. Predictive maintenance can be performed on machinery, minimizing downtime and maximizing productivity.
Healthcare
In healthcare, digital twins of human organs have been used to predict how tumors might grow or how diseases may progress, thereby aiding in personalized treatment plans. It also provides a safe environment for medical professionals to simulate and practice procedures.
Aerospace
The aerospace industry uses digital twins for the design and testing of aircraft. They can simulate flight conditions and potential issues, which can be resolved in the virtual environment before real-world testing, reducing costs and increasing safety.
Urban planning and smart cities
Cities can utilize digital twins to optimize traffic flows, plan urban development, manage energy use, and even predict or monitor the spread of diseases.
Supply Chain Management
Digital twins can simulate and optimize complex supply chain networks and the interactions between different parts. They can predict the impact of disruptions, help in planning and risk management, and enhance overall supply chain efficiency and resilience.
Components of a digital twin system
There are a huge number of pieces that compose a digital twin system. Here are some of the most important components:
- Physical object or system - The real world entity that the digital twin will represent. This can be anything from a single physical object to entire complex systems like a city.
- Sensors and IoT Devices - These are the devices that are embedded or connected to the physical entity to collect data. These are what allow a digital twin to be updated dynamically to keep its state synchronized with the physical entity.
- Network infrastructure - Network connectivity is required to transfer the data from sensors to the digital twin. For larger systems this can be extremely complex and must be secure and reliable to be effective.
- Data processing and storage - Because data for digital twin systems is often high volume and must be processed quickly, specialized tools are often used. This includes specialized databases and big data processing tools to transform or process the data prior to sending it to the digital twin model.
- Digital Twin software - This software is what takes incoming data and updates the virtual model. It can include algorithms to simulate the object, make predictions, or take action based on the current state of the model
- User interface - A UI is needed for humans to interact with the model and monitor it.
Digital twin key concepts
Physical to digital data links
A key feature of modern digital twins is the ability to update the digital twin based on data coming from sensors and IoT devices monitoring the physical twin.
Real time data
With more powerful hardware becoming available at affordable prices, real time data can be used so there is minimal deviation between the state of the digital and physical twins.
Simulation
Once an accurate digital representation of a physical object has been created, simulating how the device will behave under different conditions via simulation is a key part of digital twin technology.
FAQs
Digital twin vs. simulation
While digital twins and simulations are both tools used to model and predict the behavior of systems, there are a few differences:
- Data input - Most simulations are based on predefined data or assumptions to test a specific scenario based on these inputs. Digital twins in contrast are constantly changing due to updates based on data from sensors and IoT devices
- Interactivity - Digital twins have a live interaction with data from the real world, allowing the digital model to change based on physical data and changes to the digital twin can also be used to modify the physical entity. In comparison simulations typically take place in a fixed environment.
- Scope of model - Simulations are typically designed to answer specific questions or model specific scenarios. Digital twins are able to model an entire system and can thus be used for answering much broader questions in a more versatile way.
- Timing - Simulations are generally run for a set period of time or until a condition is met. Digital twins are updated continuously and used as long as the physical object exists and is generating data.
At the most basic level, digital twins can be seen as a more dynamic and interactive alternative to traditional simulations.
What are the types of digital twins?
There are a number of different categories to break down digital twins based on their features and how they are used. These aren’t necessarily exclusive and a digital twin model could include aspects of all of these categories.
- Product twins - Product twins are models that represent individual physical items. These are generally used for product development and testing for tasks like finding design flaws or determining the lifespan of a part. In operations they can be used for predictive maintenance and real time monitoring.
- Process twins - Process twins represent complex process like an assembly line in a factory or supply chain. By using process twins an organization can find inefficiencies, test out the impact of changes, and make predictions.
- System twins - System twins are representations of large systems like cities or entire ecosystems. They are used for strategic planning like emergency response or testing how changes impact the system.
Take charge of your operations and lower storage costs by 90%
Get Started for Free Run a Proof of ConceptNo credit card required.
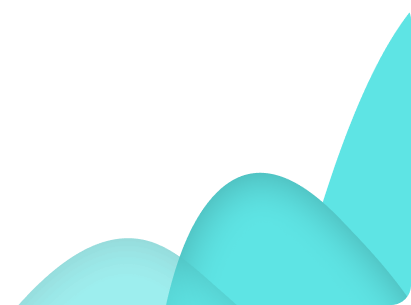