Infrastructure Monitoring with InfluxDB | Live Demonstration
SCADA (Supervisory Control And Data Acquisition)
SCADA stands for Supervisory Control and Data Acquisition. A SCADA system is usually a collection of both software and hardware components that allow supervision and control of industrial plants.
What is SCADA?
SCADA stands for Supervisory Control and Data Acquisition. A SCADA system is usually a collection of both software and hardware components that allow supervision and control of industrial plants. Most SCADA solutions try to fulfill four key roles:
- Control industrial process (locally and remotely)
- Collect and monitor real-time plant data from industrial equipment (PLC’s, sensors)
- Provide interfaces for plant workers to directly interact with sensors, pumps and motors through HMI (human-machine interface) software
- Event logging
Before SCADA systems industrial processes within plants had to be monitored and operated manually via selector switches, push buttons and dials.
Most modern SCADA systems are built with an Open Architecture design and consortiums such as the OPC Foundation are largely recognized as the authoritative body’s for developing industry standards for SCADA solutions.
How does SCADA work?
A SCADA system usually consists of RTU (Remote Terminal Unit) and PLC’s (Programmable Logic Controller). RTUs and PLCs are microprocessors that communicate with field devices (sensors, HMI’s, values, motors). The Communication data from these units are routed to the SCADA platform.
The SCADA system provides a site map for which the routed data is displayed. This could be current states of field devices (ON, OFF, CLOSED, OPEN) as well as real time sensor readings such as (temperature, speed, vibration). Further to this SCADA platforms can direct commands back to PLCs and RTUs to control the field device’s states (value ON or OFF).
It is worth noting that SCADA systems provide the ability to automate responses to commonly occurring events using conditional logic, providing the building blocks for system automation. In most cases facilities choose a hybrid version deployment of system automation and direct control.
SCADA use cases/industry examples
As stated above the SCADA system facilitates two key roles. Real Time acquisition of field device data and the ability to control physical states. SCADA systems are used for the same purpose across industries. Here are some common scenarios where SCADA systems are deployed
- Oil and Gas facilities
- Manufacturing
- Water Management
- Energy Production
Realpars has developed a great example video showcasing how a SCADA system could be deployed to a Water Treatment Plant:
Traditional vs modern SCADA
It is widely recognized there are 3 generations (some split generation 3 into a 3rd and 4th generation) of SCADA architectures:
First Generation (Monolithic Systems)
Based on mainframe systems with little to no networking capabilities. Gen1 primarily communicated with remote terminal units (RTU) using proprietary vendor protocols.
Second Generation (Distributed SCADA)
Introduction of local area network (LAN) technology and slimlining of SCADA systems. Introduced common system components for SCADA solutions (HMI’s, RTU’s and databases). Proprietary protocols were still a limiting factor.
Third Generation (Networked SCADA)
Current Generation SCADA systems Introduce open system architectures providing capabilities for third party integrations, WAN (Wide Area Network) communication.
SCADA system features
SCADA system architecture usually include 5 main elements:
Supervisory computers
Supervisory computers are the core component of a SCADA system. It refers to the computer(s) responsible for collecting and controlling field devices such as RTUs and PLCs. Supervisory computers usually consist of plant HMI’s and a historian for storing time-series data collected from the field devices.
Depending on the size of the operation the deployment of supervisory computers can vary. In smaller use cases the deployment can be as basic as one master workstation. This workstation will include the historian and HMI panels. In most modern large scale deployments there is most likely a cluster of servers and client workstations handling data collection, storage and remote control. Supervisory computers are now also being deployed within cloud architectures to support global visibility and control of facilities.
Remote Terminal Units (RTU)
An RTU is essentially a microprocessor controlled electric device that interfaces with sensors and actuators. There is quite a bit of overlap between PLCs and RTUs but one of the primary distinguishing features is their deployment placement. RTU’s are usually installed in remote areas of a facility and deploy wireless interfaces for data and collection. In most cases RTUs are directly controlled by the supervisory computers. It is also worth noting that RTUs are predominantly used for data collection rather than actuation due to the risk of signal failure, unless being paired with a PLC.
Program Logic Controllers (PLC)
PLC’s are industrial computers that also monitor sensors and control actuators. Essentially engineers deploy a series of rules and logic which controls the I/O of the industrial computer. The primary difference between PLCs and RTUs is that PLC’s in most cases can work independently from a SCADA system. PLC’s can also deploy their own local storage. Modern PLC’s can now provide IP based communication directly to SCADA systems, typically however this communication is handled by an RTU.
Communication Infrastructure
The communication backbone between the Supervisory Computers and field devices. Most facilities deploy a wireless and hardwired communication infrastructure. Depending on the SCADA system and field devices the communication protocol can vary. A standardized communication protocol for SCADA and field devices is OPC UA.
Human-machine Interface (HMI)
The HMI is the operator window of the supervisory system. Most HMI’s will mimic the process or facility schematic being monitored and controlled by the supervisor computers. Each sensor / actuator will be represented within the interface along with a real time view of the data being collected from each. This could be a state, sensor reading or an alarm. The HMI will also provide an interface for the data historian so plant engineers can review historical data being stored for each field device.
Benefits of SCADA
In most large scale facilities SCADA systems are considered a critical component of the operation. This is due to the following benefits:
- Quick response to issues - SCADA systems collect data from all field devices in near-real time. This allows site engineers to quickly identify and react to abnormal sensor readings such as low pressure, high temperature. The HMI maps are critical to this success allowing engineers to quickly identify the root cause.
- Proactive Maintenance - Further to this SCADA systems lay the grounds for proactive maintenance. Engineers can start to identify trends within their field devices. These trends can signal the End Of Life (EOL) of certain mechanical components. This allows engineers to order new parts and schedule maintenance rather than unexpected shutdowns.
- Automation - Lastly SCADA solutions provide the ability to automate processes within facility operations. This greatly reduces risks outside working hours and requires less staff to manage the day to day of the facility.
Disadvantages of SCADA
Although SCADA system development has improved greatly within in its third generation there are still some areas which need further development and improvement:
- Complexity - SCADA systems (especially at scale) are complex networks of hardware and software. It requires skilled operators and programmers to maintain a SCADA system. In many cases critical members of SCADA teams can leave facilities leaving knowledge gaps.
- Legacy Historians - One of the primary issues with SCADA systems today is the use of outdated custom historian databases. In most cases Legacy historians will derive from a SQL database like microsoft sql server and be highly tuned to ingest raw sensor data. As the SCADA systems grow (more data, more analytical demand for data) these historians fail to scale with the rest of the SCADA system.
- Legacy User Interface - Like historians, the HMI interface for SCADA systems has not greatly improved through generations. Although the current visualizations are robust it does restrict innovative views of sensor data such as heatmaps. There is also a lack of unity between the historic data from field devices and the real time readings with many solutions having completely different HMI’s for each.
Take charge of your operations and lower storage costs by 90%
Get Started for Free Run a Proof of ConceptNo credit card required.
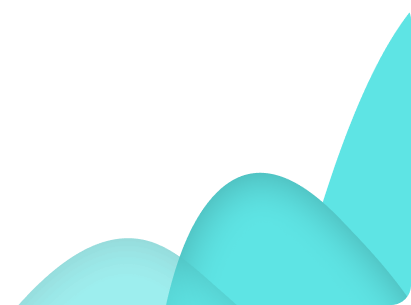